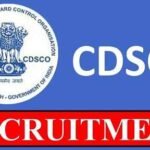
Introduction to Henkel adhesives for medical devices and their applications?

Henkel is a global leader in adhesive technologies, and its solutions for the medical device industry play a crucial role in ensuring high-performance, safe, and reliable medical devices. Henkel’s adhesives are widely used in the design, manufacturing, and assembly of medical devices, offering solutions that meet the rigorous demands of this highly regulated sector.
Introduction to Henkel Adhesives for Medical Devices:
Henkel provides a range of advanced adhesive technologies that are designed to meet the stringent requirements of the medical device industry. These adhesives are used in various applications, including implantable devices, diagnostic tools, surgical instruments, and wound care products. Henkel’s adhesive solutions are engineered for biocompatibility, durability, and ease of use, making them suitable for critical medical applications.
Key Features of Henkel Adhesives for Medical Devices:
- Biocompatibility:
- Henkel’s medical-grade adhesives are tested to meet biocompatibility standards such as those outlined by ISO 10993, ensuring that they are safe for use in contact with human tissues and body fluids.
- Biocompatible adhesives are essential for implantable devices, surgical instruments, and wound care products, as they need to ensure patient safety and minimize any risk of adverse reactions.
- Sterility:
- Many of Henkel’s medical adhesives can be sterilized by common methods, including ethylene oxide (EO), gamma radiation, and autoclaving. This is essential for ensuring that the adhesives used in medical devices remain sterile and safe for use in clinical settings.
- Precision and Strength:
- Henkel’s adhesives provide exceptional bonding strength, even in the most challenging medical environments. Whether the application is for electrical components, plastics, or metals, Henkel’s adhesives ensure robust bonding without compromising device performance.
- Micro-dispensing systems enable precise and consistent application of adhesives in high-precision medical device manufacturing.
- Fast Curing and Low-Temperature Performance:
- Many of Henkel’s adhesives offer fast-curing and low-temperature performance, which are important for medical device assembly processes that require quick turnaround times while maintaining high-quality bonding.
- Flexibility and Durability:
- Henkel’s adhesives are formulated to handle a range of mechanical stresses, ensuring that medical devices retain their integrity over time. This is critical for devices that must endure prolonged use or be exposed to the rigors of sterilization and repeated handling.
- Customization and Formulation:
- Henkel offers customizable adhesive solutions that meet specific application requirements such as viscosity, open time, and adhesion strength, allowing manufacturers to optimize performance for each unique medical device.
- The company also provides adhesive formulations for different types of materials, such as plastics, metals, ceramics, and silicone, commonly used in medical devices.
Applications of Henkel Adhesives in Medical Devices:
Henkel adhesives are used in a wide array of medical device applications, ranging from implantable devices to diagnostic equipment. Some key applications include:
1. Implantable Devices:
- Orthopedic implants (e.g., hip replacements, knee implants, bone screws, and spinal implants) rely on high-performance adhesives for bonding metal, polymer, and ceramic components securely.
- Cardiovascular implants, such as pacemakers or stents, require adhesives that can withstand constant movement, biological fluids, and long-term implantation within the body.
2. Wound Care Products:
- Henkel’s adhesives are widely used in bandages, dressing tapes, wound closure devices, and hydrocolloid dressings. These adhesives must be gentle on the skin, water-resistant, and capable of holding the wound dressing in place without causing irritation or allergic reactions.
- The skin-safe adhesives help ensure proper adhesion and ease of use, reducing the risk of skin damage when applied or removed.
3. Diagnostic Devices:
- Adhesives are critical in the manufacture of diagnostic devices such as biosensors, test strips, catheters, and blood glucose monitors. Henkel adhesives provide the strong bonds needed to hold together the intricate components of diagnostic devices, including electronics and biosensors, ensuring accurate and reliable performance.
- Flexible electronics for diagnostic wearables are another example where Henkel adhesives help form durable, skin-friendly bonds for devices that need to remain attached to the body during use.
4. Surgical Instruments:
- Adhesives are used in the assembly of surgical tools, endoscopes, and catheters, where precision and clean handling are required. Henkel adhesives support the assembly of devices that must be sterilized and used in sterile environments while maintaining high bonding strength.
- Biocompatible coatings for surgical instruments are also a key use of Henkel adhesives, allowing for non-stick surfaces or coatings that improve device performance during procedures.
5. Drug Delivery Systems:
- In transdermal drug delivery systems, Henkel adhesives are used to bond active pharmaceutical ingredients (APIs) with the adhesive matrix for effective and controlled release. These adhesives need to provide a secure bond while ensuring that the active ingredients are delivered efficiently to the patient.
- Patches and other drug delivery devices rely on these adhesives to maintain integrity while also ensuring comfort and long-term wearability.
6. Electronics and Medical Sensors:
- Medical wearables and sensors, such as those used in continuous monitoring of vital signs (e.g., blood pressure, ECG, blood glucose), often rely on Henkel’s conductive adhesives. These adhesives ensure that electrical connections between components are maintained while maintaining the safety and comfort of the wearer.
- Flexible substrates in medical electronics are also an important application where Henkel adhesives provide reliable bonding, even for curved or stretchable devices.
7. Packaging for Medical Devices:
- Henkel adhesives are also used in the packaging of medical devices, ensuring tamper-proof seals and sterile barriers that protect the device until use.
- Sealing and bonding for medical packaging materials, including blister packs, pouches, and cartons, ensure that the device remains safe and sterile during transportation and storage.
Henkel’s Product Offerings for Medical Device Manufacturing:
Henkel offers a range of products tailored to medical device manufacturing needs, including:
- Loctite®: A well-known brand of adhesives and sealants that offers solutions for a variety of medical applications, including bonding, sealing, and conformal coatings.
- Technomelt®: A family of hot melt adhesives that offer fast curing, strong adhesion, and flexibility, ideal for wound care, drug delivery, and assembly.
- Hysol®: Epoxy adhesives that provide strong, durable bonds in high-stress environments, often used in implantable devices and surgical instruments.
- Araldite®: A range of structural adhesives ideal for bonding metals, plastics, and composites used in medical device assembly.
- Permabond®: A brand that includes cyanoacrylate adhesives and anaerobic adhesives for rapid bonding in medical applications requiring fast setting times and strong adhesion.
Henkel adhesives are integral to the design and production of high-performance medical devices. Their focus on biocompatibility, sterilization resistance, and precision bonding makes them suitable for a wide range of medical applications, from implantable devices and wound care products to diagnostic tools and drug delivery systems. Henkel’s innovations in adhesive technologies not only meet the complex demands of the medical device industry but also support manufacturers in complying with stringent regulatory requirements while ensuring patient safety and device efficacy.