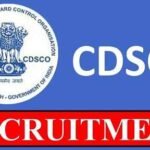
How do you manage costs for custom or specialized components in Medical Device ?
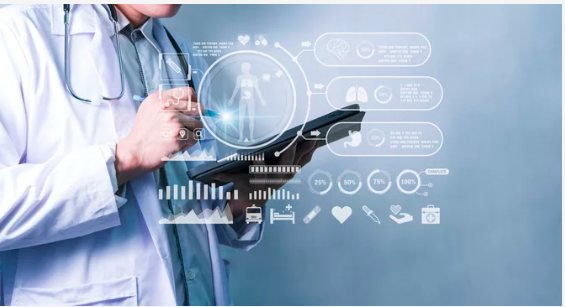
Managing costs for custom or specialized components in medical device manufacturing requires strategic planning, efficient design and production processes, and careful supplier management. Here’s how companies typically approach cost management for these critical parts:
1. Early Supplier Involvement
- Collaboration: Engaging suppliers early in the design process can provide insights into the cost implications of design decisions and allow for adjustments that balance performance with cost.
- Design for Manufacturability (DFM): Work with suppliers to modify designs to simplify manufacturing processes, reduce material waste, and lower production costs without compromising the quality or functionality of the device.
2. Volume Forecasting and Planning
- Accurate Forecasting: Develop accurate forecasts for component demand to optimize production runs and reduce costs through economies of scale.
- Long-term Contracts: Negotiate long-term contracts with suppliers to secure better pricing on materials and components, based on stable, projected volumes.
3. Material Selection and Substitution
- Cost-effective Materials: Evaluate and select materials that provide the necessary functional properties at a lower cost whenever possible.
- Material Substitution: Continuously seek alternative materials that may reduce costs without affecting product performance, particularly in response to fluctuations in raw material prices.
4. Value Engineering
- Component Consolidation: Reduce the number of unique components in a device by combining parts or functions, which can simplify assembly and reduce inventory costs.
- Standardization: Where possible, standardize components across multiple product lines to increase purchasing power and reduce costs.
5. Technological Investments
- Automation: Invest in automation for the production of high-volume or complex components to decrease labor costs and improve production consistency.
- Advanced Manufacturing Techniques: Utilize advanced manufacturing techniques such as additive manufacturing (3D printing) to produce complex components at potentially lower costs, especially for low-volume production where traditional tooling costs would be prohibitive.
6. Supplier Management
- Strategic Sourcing: Identify and collaborate with strategic partners who can offer competitive pricing, reliable delivery, and high quality. Diversifying the supplier base can also mitigate risks and leverage competitive pricing.
- Supplier Audits and Performance Reviews: Regularly review supplier performance to ensure they meet cost, quality, and delivery targets. Use audits to identify areas for improvement and cost reduction.
7. Lean Manufacturing
- Waste Reduction: Implement lean manufacturing principles to minimize waste in every aspect of the production process, from raw material usage to energy consumption.
- Continuous Improvement: Foster a culture of continuous improvement where employees at all levels are encouraged to suggest ways to reduce costs and enhance efficiency.
8. Inventory Management
- Just-In-Time (JIT) Inventory: Reduce inventory holding costs by implementing JIT inventory systems that ensure components are delivered as they are needed.
- Inventory Optimization: Use inventory management software to optimize stock levels and reduce excess inventory, which ties up capital and incurs storage costs.
9. Total Cost of Ownership (TCO) Analysis
- Holistic Cost Analysis: Consider all aspects of the component lifecycle, including initial costs, maintenance, and potential end-of-life disposal costs. This comprehensive analysis can sometimes justify a higher initial cost in exchange for lower long-term expenses.
10. Regulatory and Compliance Considerations
- Compliance Costs: Factor in the costs associated with regulatory compliance, which can affect material choices and supplier selection, particularly for medical devices that require biocompatibility and sterilization.