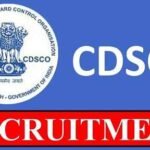
How do medical device manufacturers ensure product quality?
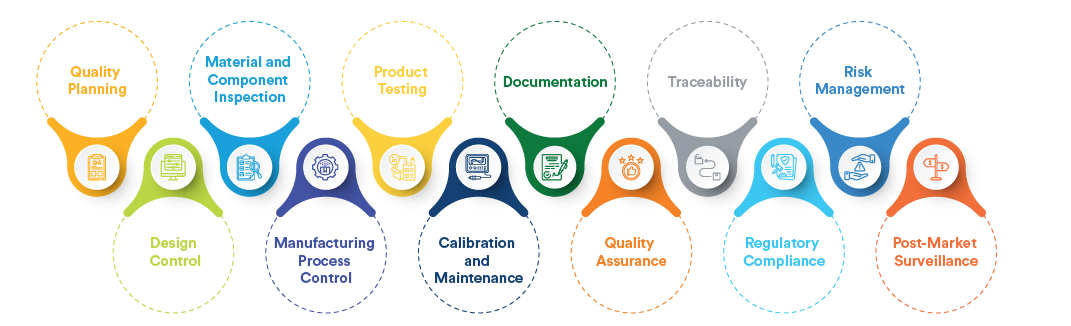
Ensuring product quality is paramount for medical device manufacturers, as it directly impacts patient safety, regulatory compliance, and market success. Manufacturers implement a comprehensive strategy involving robust systems, processes, and tools to ensure that devices meet stringent quality standards at every stage of their lifecycle. Here’s how they achieve this:
1. Quality Management System (QMS):
- Compliance with Standards:
- Most manufacturers adopt QMS frameworks like ISO 13485 to ensure consistent quality across all processes.
- FDA’s 21 CFR Part 820 outlines QMS requirements for manufacturers selling in the U.S.
- Scope: A QMS covers design, manufacturing, testing, packaging, labeling, storage, and distribution.
- Continuous Improvement: Regular audits and reviews ensure the QMS remains effective and up-to-date.
2. Risk Management:
- ISO 14971 Compliance: A risk management process identifies, evaluates, and mitigates potential risks throughout the product lifecycle.
- Risk Assessments:
- Failure Modes and Effects Analysis (FMEA).
- Hazard analysis to ensure risks are within acceptable limits.
- Post-Market Risk Monitoring: Collecting real-world data to address risks that arise after product launch.
3. Design and Development Controls:
- Design Input: Incorporating user needs, regulatory requirements, and performance specifications.
- Design Verification: Ensuring the design meets specified requirements.
- Design Validation: Testing prototypes under real-world conditions to confirm they fulfill user needs.
- Design Reviews: Regular assessments by cross-functional teams to identify and resolve issues early.
4. Supplier and Material Management:
- Supplier Qualification: Evaluating and selecting suppliers based on their ability to meet quality and regulatory standards.
- Incoming Material Inspection:
- Testing raw materials and components for quality and compliance.
- Ensuring materials meet medical-grade requirements (e.g., biocompatibility, durability).
- Supplier Audits: Regularly auditing suppliers to ensure ongoing adherence to quality standards.
5. Manufacturing Process Controls:
- Standard Operating Procedures (SOPs):
- Detailed documentation of manufacturing processes to ensure consistency.
- Process Validation:
- Ensuring production processes consistently produce devices meeting predetermined specifications.
- Examples include IQ (Installation Qualification), OQ (Operational Qualification), and PQ (Performance Qualification).
- Automation and Robotics:
- Reducing human error and improving precision through automated manufacturing.
6. Cleanroom and Environmental Controls:
- Controlled Environments: Manufacturing devices in cleanrooms to prevent contamination, especially for sterile or implantable devices.
- Environmental Monitoring: Regular testing of air quality, temperature, and humidity to maintain standards.
7. Testing and Inspection:
- In-Process Testing:
- Inspecting components and assemblies at various stages of production.
- Final Product Testing:
- Functional tests to ensure the device performs as intended.
- Safety tests, such as electrical safety for powered devices.
- Sterility and biocompatibility tests for applicable devices.
- Documentation: Recording all testing results for traceability and regulatory compliance.
8. Documentation and Traceability:
- Device Master Record (DMR):
- Detailed documentation of manufacturing processes, materials, and specifications.
- Device History Record (DHR):
- Records of each device’s production, testing, and release to ensure traceability.
- Unique Device Identification (UDI):
- Assigning a unique identifier to each device for tracking and recall purposes.
9. Employee Training and Competency:
- Skill Development: Regular training programs ensure employees are familiar with QMS, regulatory requirements, and technical processes.
- Competency Verification: Periodic assessments to confirm staff can perform tasks to required standards.
10. Regulatory Compliance:
- Pre-Market Approval:
- Adhering to regulatory requirements during design and testing phases.
- Examples: FDA 510(k) clearance or PMA (Pre-Market Approval), CE marking in the EU.
- Post-Market Surveillance:
- Monitoring device performance and adverse events after market launch.
- Reporting and addressing issues as per regulatory guidelines.
11. Automation and Technology Integration:
- Digital Quality Management Systems (e-QMS):
- Streamlining processes, documentation, and audits using digital platforms.
- Data Analytics:
- Using AI and machine learning to identify trends and predict potential quality issues.
- Connected Devices:
- IoT-enabled devices provide real-time performance data, enabling proactive quality monitoring.
12. Internal and External Audits:
- Regular Audits:
- Internal audits to ensure adherence to company policies and regulatory requirements.
- External audits by regulatory bodies or notified bodies to confirm compliance.
- Audit Follow-Up:
- Addressing findings and implementing corrective actions promptly.
13. Customer Feedback and Complaint Handling:
- Customer Feedback Systems: Collecting and analyzing feedback to identify quality concerns.
- Complaint Resolution:
- Investigating complaints and implementing corrective actions.
- Reporting serious incidents to regulatory authorities.
14. Recalls and Corrective Actions:
- Recall Readiness: Developing processes for rapid response to quality or safety issues.
- Corrective and Preventive Actions (CAPA):
- Identifying root causes of quality issues.
- Implementing measures to prevent recurrence.
15. Focus on Continuous Improvement:
- Lean Manufacturing: Reducing waste and improving efficiency without compromising quality.
- Six Sigma: Using data-driven methodologies to improve processes and reduce defects.
- Kaizen: Encouraging small, continuous improvements at all levels.
Medical device manufacturers ensure product quality through a combination of robust quality management systems, rigorous testing, supplier oversight, and adherence to regulatory standards. By integrating advanced technologies and fostering a culture of continuous improvement, manufacturers can deliver safe, effective, and reliable medical devices that meet both clinical and regulatory demands.