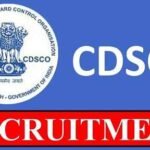
Can you provide a cost breakdown for development and production in Medical Device?
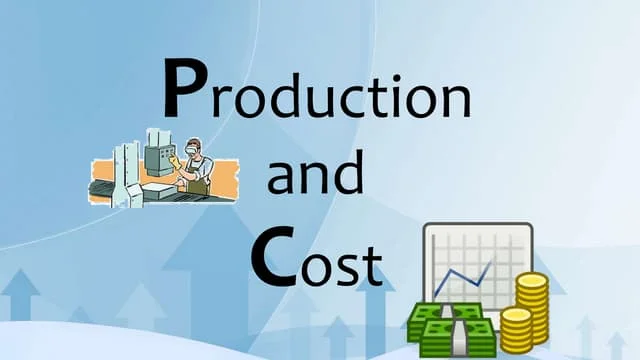
Providing a cost breakdown for the development and production of medical devices involves considering various stages and factors, as costs can vary significantly depending on the complexity of the device, regulatory pathway, materials used, and the scale of production. Below is a general outline of key cost components involved in medical device development and production:
1. Concept and Design Phase
- Research and Development (R&D): Initial expenses include market research, feasibility studies, and preliminary design. This phase may require hiring specialists, consultants, or leveraging in-house R&D teams.
- Prototyping: Costs associated with materials and manufacturing methods to create prototypes. Rapid prototyping technologies like 3D printing can help reduce these costs.
- Design Iteration: Expenses incurred in refining prototypes based on testing and feedback.
2. Regulatory Compliance and Testing
- Preclinical Testing: Laboratory testing and other validation processes to ensure the device performs safely and as intended.
- Regulatory Submission Fees: Costs associated with preparing and submitting regulatory documentation, such as FDA 510(k) submissions or CE marking applications.
- Clinical Trials: If required, clinical trials can be a significant expense, including costs for patient recruitment, site management, and data analysis.
3. Manufacturing Setup
- Tooling and Equipment: Investment in manufacturing tools and equipment, which can be substantial for custom or complex devices.
- Manufacturing Process Development: Costs to develop and validate the manufacturing process, including quality control systems.
4. Material and Production Costs
- Raw Materials: Costs of materials used in the manufacture of the device.
- Production Labor: Labor costs associated with the production line.
- Quality Assurance and Control: Ongoing costs for quality testing and compliance during production.
5. Packaging and Sterilization
- Packaging Design and Production: Costs for developing and producing packaging that meets regulatory and market requirements.
- Sterilization: Costs for sterilizing the devices before shipment, if applicable.
6. Distribution and Marketing
- Logistics: Costs for storage, handling, and shipping of the devices.
- Marketing and Sales: Expenses related to marketing campaigns, sales staff, product launches, and promotional materials.
7. Post-Market Surveillance and Maintenance
- Post-Market Studies: Ongoing costs associated with post-market surveillance required by regulatory bodies.
- Product Support and Maintenance: Costs for customer support, warranty provisions, and potential product recalls or updates.