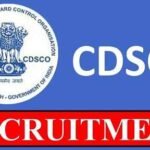
Are you experienced with 3D printing or additive manufacturing in Medical Devices?
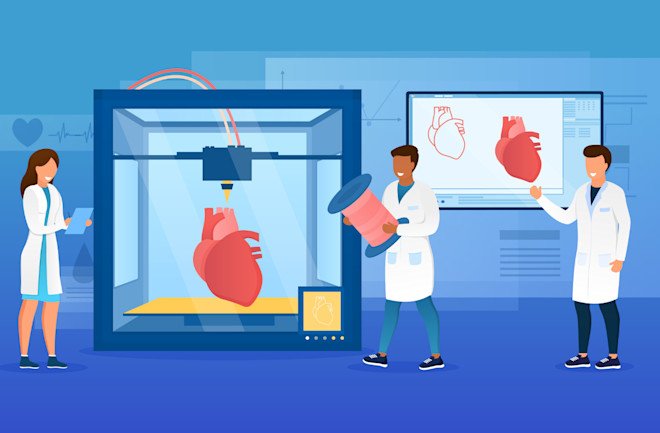
This technology plays a crucial role in prototyping, designing, and manufacturing various medical devices and components. Here’s an overview of its applications, benefits, and considerations:
Applications of 3D Printing in Medical Devices
- Prototyping: 3D printing is extensively used for rapid prototyping, allowing engineers and designers to quickly create and iterate device prototypes, thus speeding up the development process and testing phases.
- Custom Implants and Prosthetics: Customized implants and prosthetics can be manufactured to fit the unique anatomical features of individual patients, improving comfort and functionality. This includes items like orthopedic implants, cranial plates, and custom dental restorations.
- Surgical Tools and Guides: Surgeons use 3D-printed surgical tools and patient-specific surgical guides to increase the accuracy and efficiency of surgical procedures. These tools are designed to fit patient-specific anatomy, which can be derived from medical imaging data.
- Bioprinting: Although still largely experimental, bioprinting involves creating tissue and organ structures that can be used for testing drugs or, in the future, for actual organ replacement.
- Complex Device Manufacturing: Devices with complex geometries that are difficult or impossible to manufacture using traditional methods can be produced through 3D printing, allowing for more sophisticated designs and functionalities.
Benefits of 3D Printing in Medical Devices
- Customization: High degree of customization without the cost penalties associated with traditional manufacturing methods.
- Reduced Time to Market: Rapid prototyping speeds up the design process and the time to bring a medical device to market.
- Cost-Effectiveness: Reduces the cost of creating complex tools and prototypes as no special tooling is required, minimizing waste material.
- Material Diversity: Compatible with a wide range of materials, including plastics, metals, and increasingly, composite and biocompatible materials.
Considerations and Challenges
- Material Properties: Not all 3D printed materials have the same mechanical and physical properties as their traditionally manufactured counterparts. Ensuring that the materials used are suitable for their intended medical applications is critical.
- Regulatory Approvals: Medical devices produced via 3D printing must undergo rigorous regulatory scrutiny to ensure they are safe and effective. The FDA and other regulatory bodies are still evolving guidelines specific to 3D printed devices.
- Quality Control: Establishing standardized quality control procedures can be more challenging with 3D printed objects, particularly because of variability in the printing process and material properties.
Regulatory Environment
- FDA Guidance: The FDA has issued guidance that outlines the technical considerations specific to 3D-printed medical devices, covering aspects from device design, testing to quality control. Manufacturers must adhere to these guidelines to ensure compliance and approval.
Future Directions
- Advanced Materials: Research continues into advanced biocompatible materials for 3D printing that can provide better durability, flexibility, and integration with the human body.
- Increased Adoption: As the technology matures and costs continue to decrease, the use of 3D printing in medical devices is expected to grow, further broadening the types and complexities of devices that can be produced.